I spent some time pondering the heated seat situation and even studied how relays work before deciding that I will fit them without relays and run the wiring along the main front to rear loom and whilst I was at it run a spare wire for any future requirements that I may have.
I had bought 5 of these lovely switches some time ago which is handy as I need 3 of them now. One for the electric fan and two for the seats. A long time ago I had installed one in a hole that I had on the support for the dashboard. I didn't realise that the hole wasn't original until the car was painted otherwise I would have welded it up and the switch fitted perfectly. I guess the hole was a leftover of an upgrade that a previous owner had done.
I spent ages measuring up the various lengths of wire required before soldering the switches on and then wrapping them in loom tape, all very enjoyable. This is the finished harness.
Once installed I decided against putting the holes into the rear seat panel until I knew where the wires from the seat will be so this is the three wires coiled up and waiting for final fitment.
I quite like the look of the switches and when the doors are closed they are hard to see from outside of the car but easy to access from the inside.
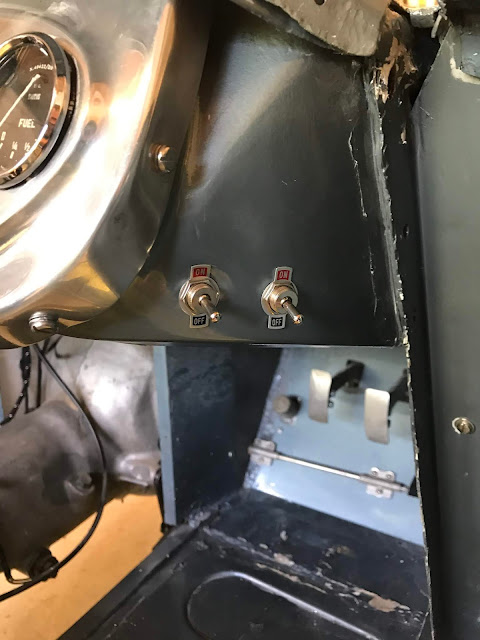
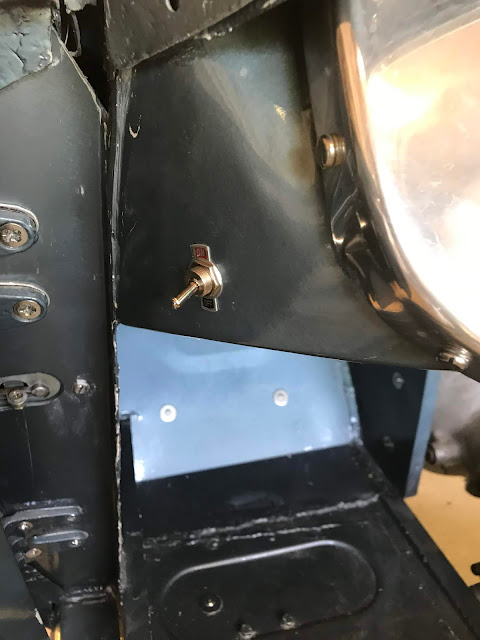
I got round to fitting Rivinuts to the underside of the chassis and properly tying up the main lead from the battery to the starter which has been dragging on the floor for ages. I did whilst fitting the seat harness. I'd jacked up the car to do this so started on the other jobs I had on the underside which included fitting the gearbox support stay with its bushes. I had it installed a long time ago, in fact when I installed the engine as I needed it to push the engine forward to get it line up with the engine mounting bolts on the chassis. I was a little worried that when I undid the nuts that the engine would slide backwards but to my surprise it didn't. I had read an article some years ago on this job and it majored on the importance of putting a collar inside the hole in the gearbox plate as the hole is much bigger than the stay bar. was so taken with the article that I screen shotted it and have been looking at it on my desktop ever since. I remembered the collar but forgot to put two nuts on the inside though and wish I had used nyloc nuts on the ends of the bar. I have ordered some and will strip it all down again to put the nuts in the correct position. I am also a little concerned that I may have cut the bar too short and I don't think I have any more so perhaps this will be something I come back to much latter on. However, it was easy to do and is something I am happy to have at this stage.
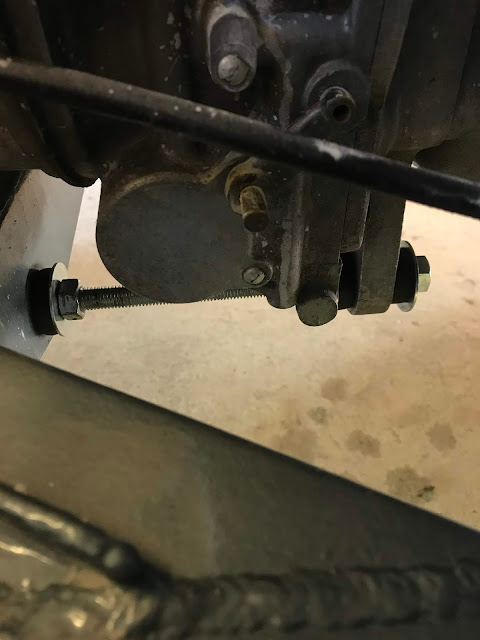
One of the other jobs I need to do is adjust the brakes so I took the front wheel off and did those before I got distracted by the wiring of the lights which was hanging loose and flapping freely. I have made a start on that.